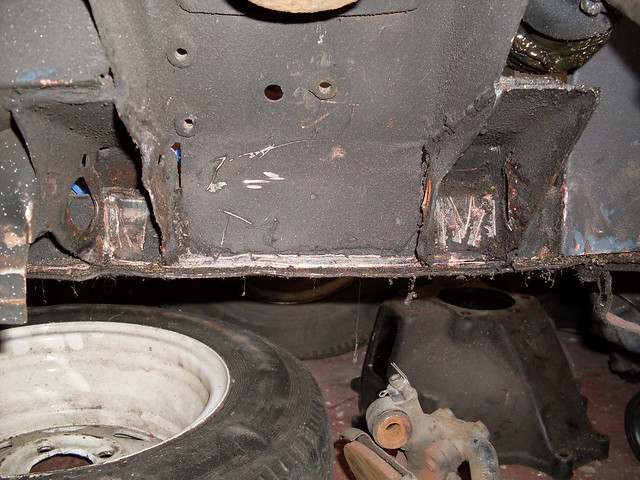
I started off cutting back the front bracket and it's supporting plate back. But I soon ran into an unexpected, but minor, problem. Part way through cutting the bracket back, I found that it was both cracked through above the chassis rail, and on the verge of removing itself from the rail altogether.
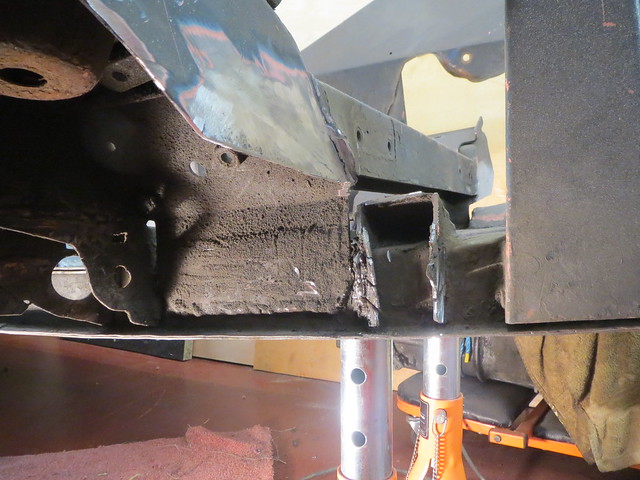
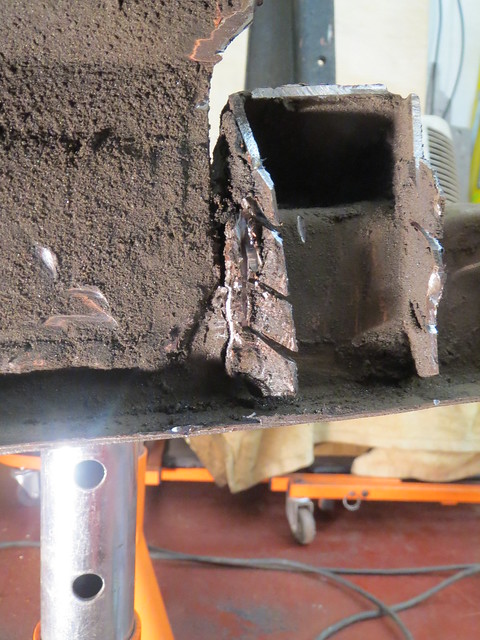
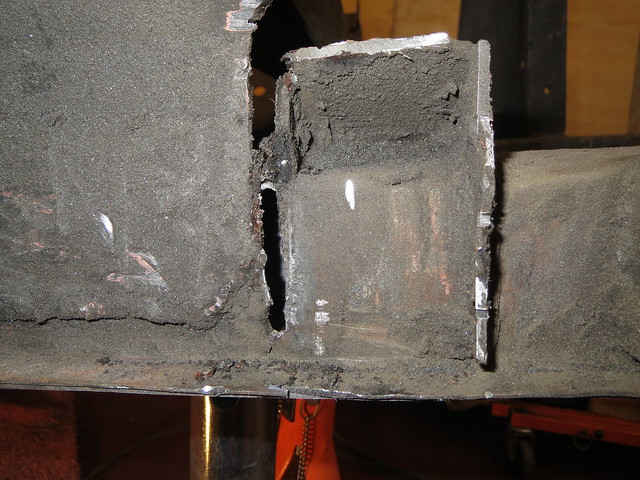
Thankfully, the tear is almost on top of one of the inner webs that I fitted when I straightened the rails so welding it up was nice and easy.
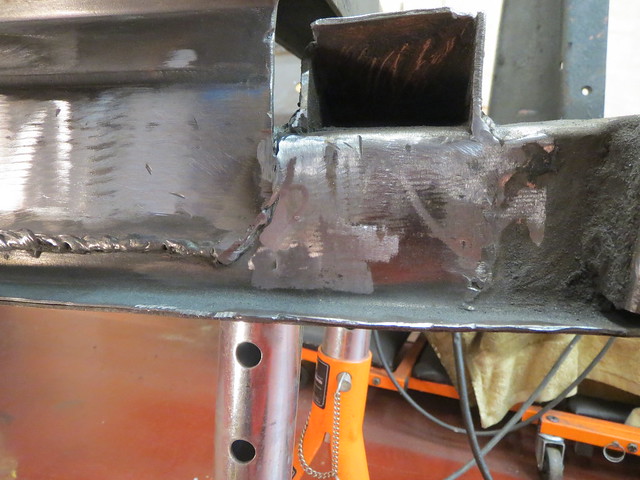
The rear half of things was next. It started off looking a bit worse for wear:
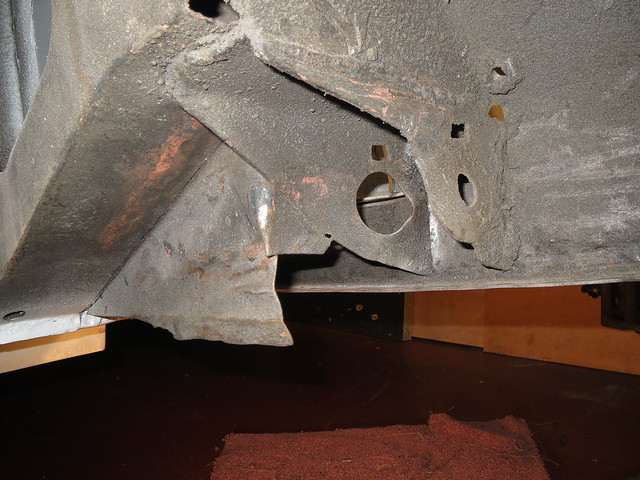
Once I'd cut back most of the unwanted sections, and given it all a clean up there was the rippled section left to flatten. The remaining bits were then cut back as far as I could get them:
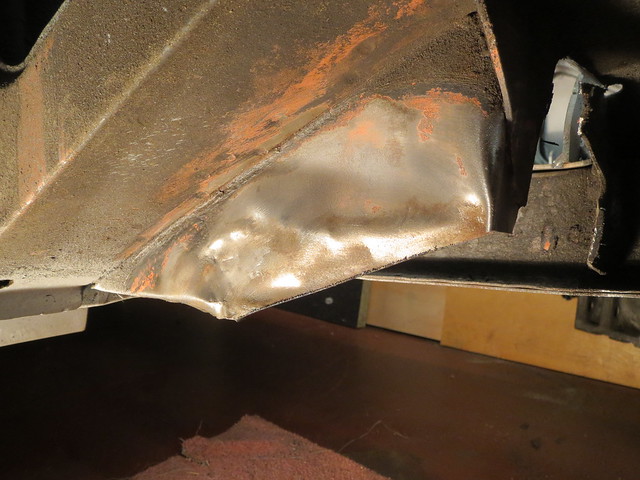
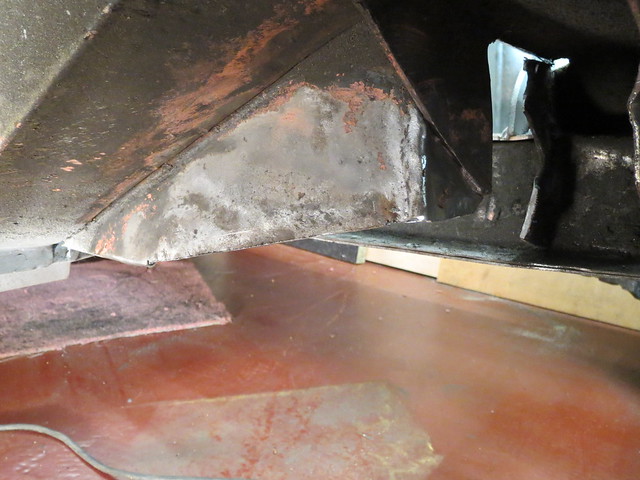
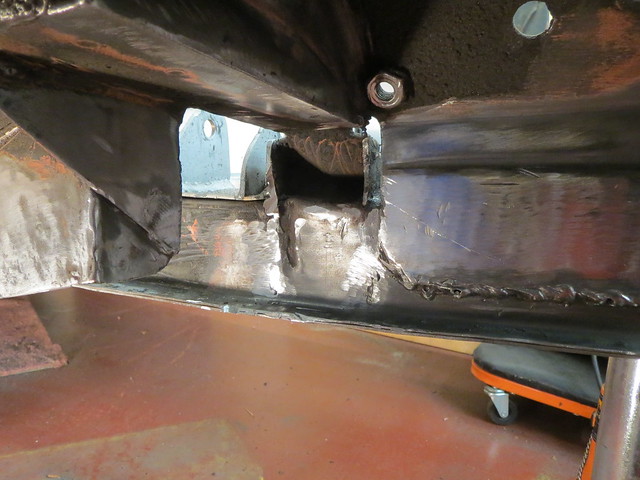
So now I had a good clean base for the suspension. This side will be built up and checked as thoroughly as I know how to before using it to make a jig for both of the suspension arms. That way I can ensure it's all even, and should I ever bin it I can make new ones easily. Before I could start with the brackets on the car, I wanted to make sure the hubs and wheel fitted together ok. They're also needed to measure the length needed for the lower arm, as it will be determined by the track width.
The front end is based on the uprights/hubs of a classic mini, but using the later Metro drive flanges as they're bigger. The usual PCD of a mini/metro is 4 x 4", ie 4 wheel studs spaced evenly on a 4" circle. My rear suspension, and wheels, use the Ford pattern of 4 x 108mm. Small differences can be taken up with special bolts, but the 6.4mm difference I have is too much for that. So the only real option is to re-drill the drive flange to suit the wider spacing. This isn't something I was willing to attempt, as the holes must be bang on and very closely sized to the splines on the new studs. But thankfully there's a local place that was happy to alter them for me, as well as trim my CV joints down to save some extra weight.
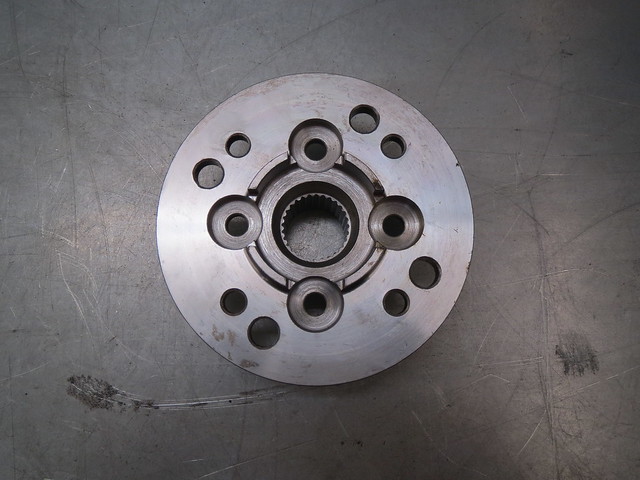
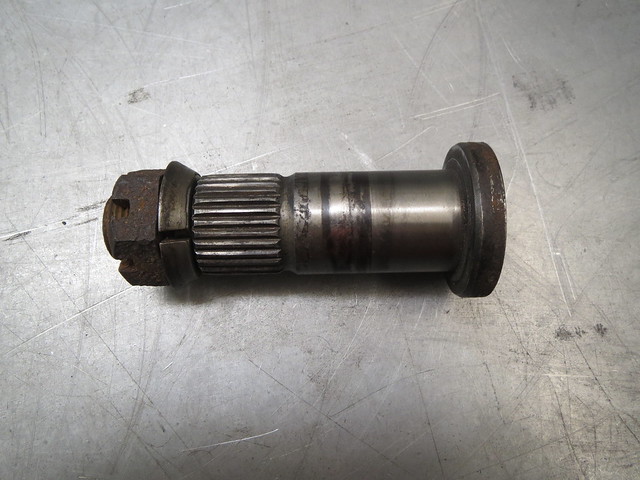
The next thing to do was to fit the new studs. The mini studs are 3/8" where as the new ones are M12, so quite a bit bigger. Which is a good thing as the Sprite will have a top speed well in excess of a mini! The easiest way I know of to fit studs is to go find a man with a press, but by this time all the local garages were shut, so I used a more manual method using a spare wheel nut and some washers. As the nut is turned the stud is drawn into the flange.
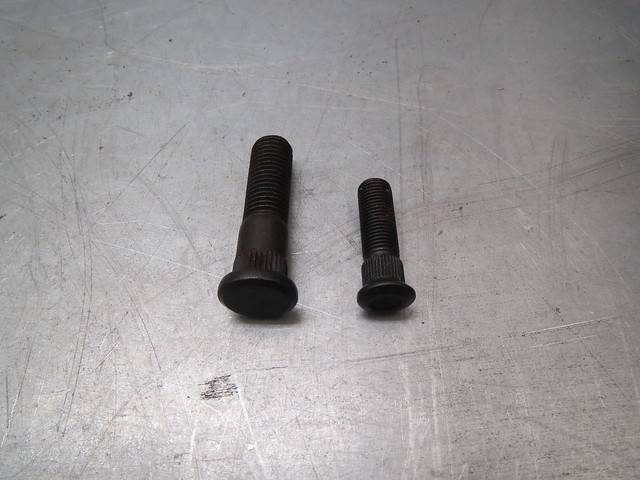
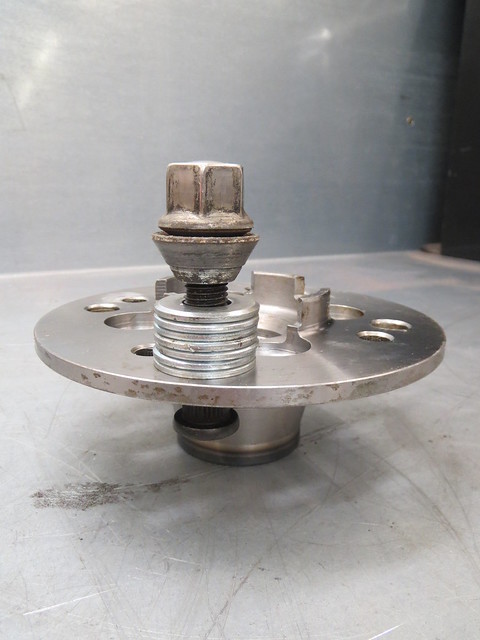
With all eight studs fitted, bearings were fitted to the upright. These are just plain ball bearings for now, as I'll be using the better, but more expensive, taper roller bearings for the final build up. The same is true of the ball joints, cheapo versions for now. The axle stub then goes in before putting the drive flange on. It looks a little long once assembled as the brake discs sits behind the drive flange. And as I'll be using 10.75" MGB discs they'll be an adaptor to match the threads that sits between the flange and disc. I'm using the hubs swapped side to side, as a mini has it's steering rack behind the wheels, where as the Sprite has it in front. This stops the brakes and steering trying to share the same space, but has no effect on the suspension itself.
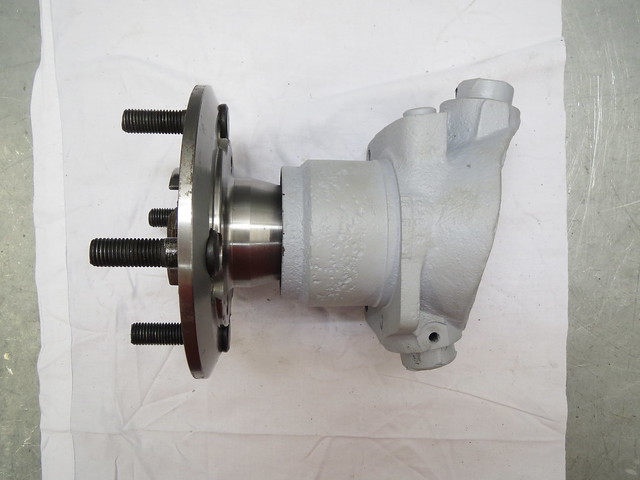

So the front uprights were now fitted and I was happy with that end of things. And that meant the last thing to do today was to spend a while levelling the suspension brackets and tacking them in place. I say levelling, as the front chassis rails kick upwards on a Sprite by 1" to give extra castor. However, my set up won't need that so the brackets are level to the ground and not the rails, hence why they look wonky. The brackets are also fitted as wide as possible, given the webs hidden inside the chassis rail. This gives the strongest possible base for the lower arm without completely re-building the front end again.
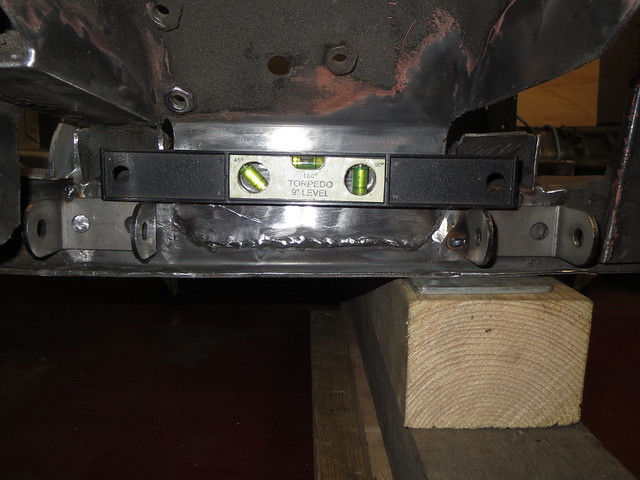
No comments:
Post a Comment