So I set about marking the plates for where I thought it best to put the strip and therefore the loads. This gave the best compromise between leading straight off the short section of tube and allowing room to fit the captive nuts later on.
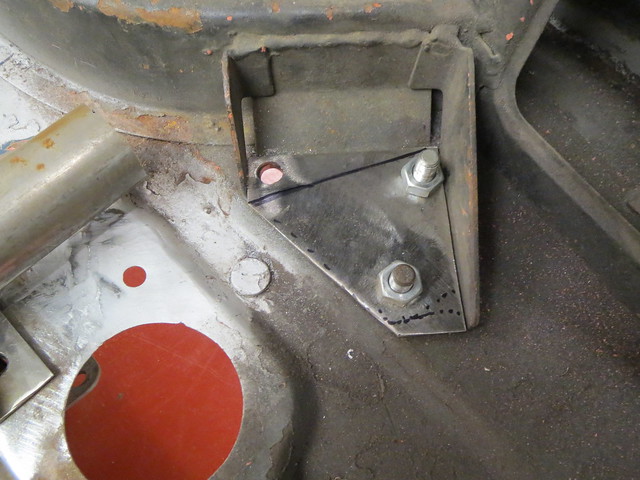
It was then on with cutting a 3mm strip overlength so I could trim it back and not risk screwing up the bends. Once I was happy with the shape, it was welded on. The sides were then cut with a slight taper and the sharp corners rounded off too.
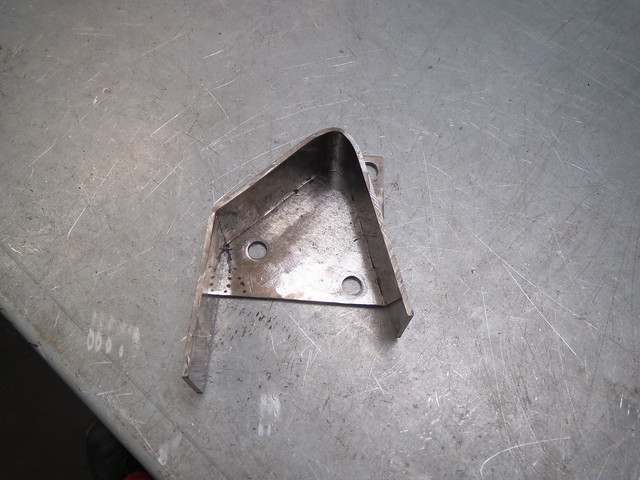
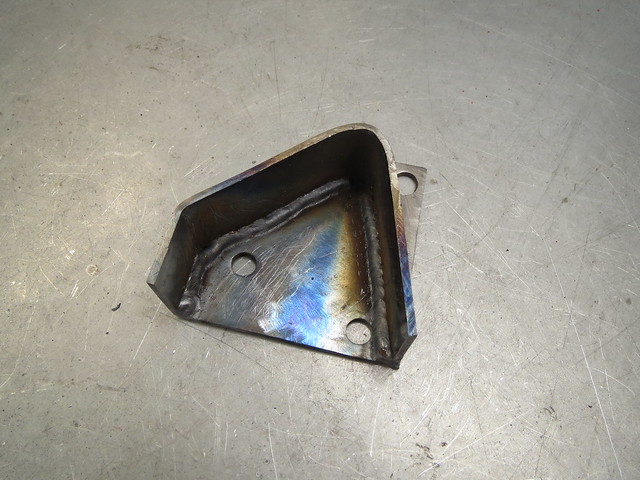
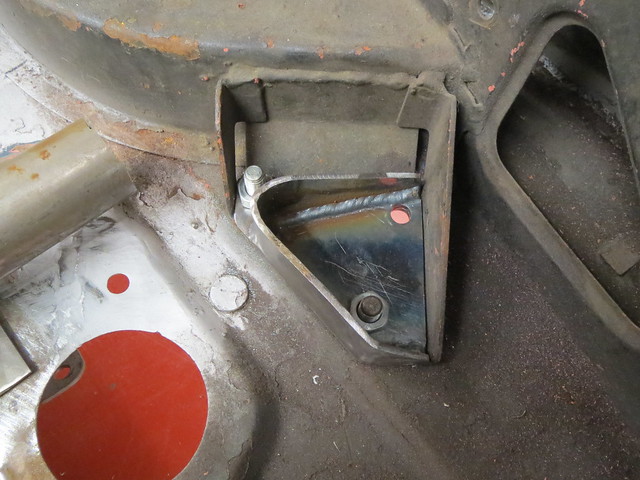
With the chassis plate now in place, I managed to find an off cut of tube with just about the right shaped cut on it. This was fitted properly and then a copy was made before I tacked the right hand piece in place. Once tacked, it was removed for welding on the bench. If I were to make this again, I'd probably weld the tubes together and then fit the feet as I can't quite fully weld the left hand side of the joining section. Given the large weld area it won't matter, but it annoys me a little bit that it's not complete.
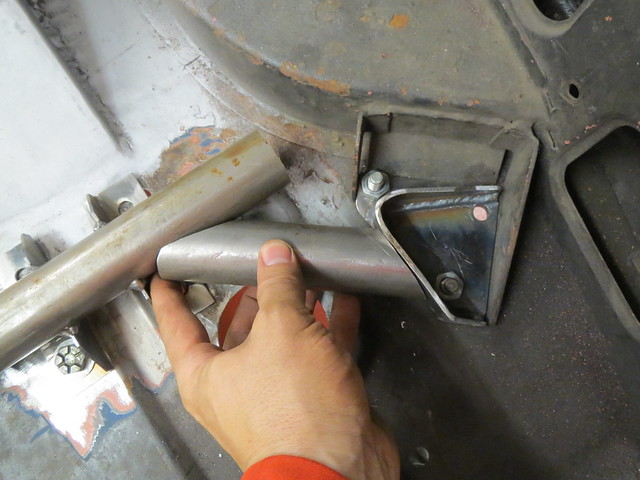
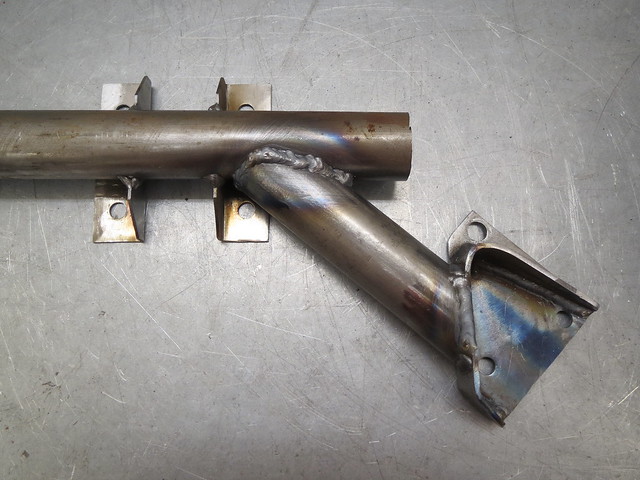
Once I have the other end welded on, I will cut the excess tube off and probably cap the ends as I saved the cut outs from when I cut the feet brackets. Once I get the tube complete I can then finally get rear wheels on. I had planned on doing this earlier in the week, but everything seems to have taken so much longer than expected. Hell, even helping a mate fit a flue liner on Wednesday involved pulling bricks out the top of the chimney 3 floors up!